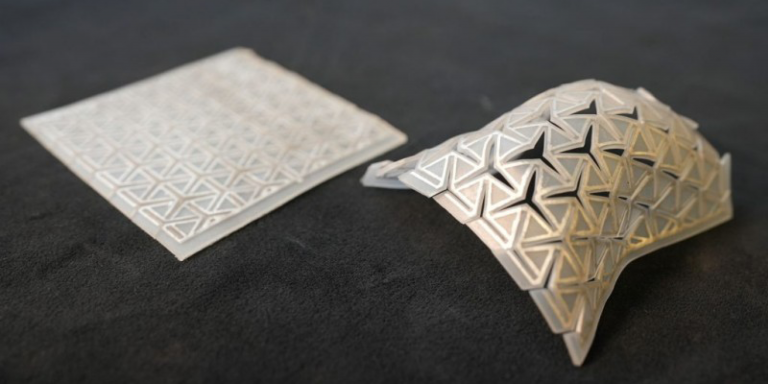
Researchers at Virginia Tech University (Virginia Polytechnic Institute and State University), located in Blacksburg, have created a robot that can transform itself and then return to its original morphology. They were inspired by the art of kirigami to design its architecture and used rubber into which they embedded a low-melting metal alloy for this innovative approach. They published their study titled “Shaping mechanical metamaterials by morphing through reversible plasticity” in Sciences Robotics last month.
Soft robotics has emerged in the last decade, thanks to the development of new soft materials like silicone and the advent of 3D printers. Researchers in this field are often inspired by nature, elephant trunks, mollusks or plants. A team at Harvard University developed the first fully soft robot in 2016 named “octobot” which takes the form of an octopus. Made of silicone from a 3D printer,it uses gas pressure to contract its tentacles. The Virginia Tech team, led by Michael Bartlett, assistant professor of mechanical engineering, also including graduate students Dohgyu Hwang and Edward J. Barron III and ABM postdoctoral researcher Tahidul Haque, took an innovative approach to shape change in the material used. Michael Bartlett explains:
“When we started the project, we wanted to get a material that could do three things: change shape, hold that shape, and then return to the original configuration, and do it over multiple cycles. One of the challenges was to create a material that was flexible enough to change shape dramatically, but rigid enough to create adaptable machines that could perform different functions.”
A kirigami-inspired transformation
Robot development is sometimes inspired by origami folding; the technique is also used in soft robotics, such as when the Harvard and MIT teams designed artificial muscles in 2017. Michael Bartlett’s team, meanwhile, has been interested in kirigami, the art of creating new shapes by cutting paper to design a structure that can be transformed.
An innovative material
They then had to invent a material that could be transformed but also return to its initial form on demand. To do this, they introduced an endoskeleton made of a low melting point alloy (LMPA) inside a rubber skin. Normally, when a metal is overstretched, the metal becomes permanently bent, cracked or stretched into a fixed, unusable shape. However, thanks to this alloy, this material, when stretched, quickly retains the desired shape.
To return the structure to its original shape, the team incorporated flexible, tendril-shaped radiators next to the LMPA mesh that causes the metal to convert to liquid at 60 degrees Celsius (140 degrees Fahrenheit), which is 10 percent of the melting temperature of aluminum. The elastomeric skin holds the molten metal in place, then returns the material to its original shape, reversing the stretch, giving the composite what the researchers call “reversible plasticity.” After cooling, the metal again helps maintain the shape of the structure. Doghyu Hwang explains:
“These composites have a metal endoskeleton embedded in a rubber with flexible heating elements, where kirigami-inspired cuts define a network of metal beams. These cuts combined with the unique material properties were really important to transform, shape quickly, and then return to the original shape.”
The researchers found that this kirigami-inspired composite design could create complex shapes, from cylinders to balls to bumpy forms. The shape change could also be achieved quickly: after impact with a bullet, the shape changed and set in less than 1/10 of a second. Moreover, if the material broke, it could be repaired several times by melting and reforming the metal endoskeleton.
One soft robot for land and air, another for sea
The team is just beginning to develop applications for this new technology. By combining the material with on-board power, control and motors, they have succeeded in creating a functional drone that autonomously transforms from a land vehicle to an air vehicle, but also a small deployable submarine, using morphing and feedback from the material to retrieve objects from an aquarium by scraping the belly of the submarine along the bottom. Edward J. Barron concludes:
“We are excited about the opportunities this material presents for multifunctional robots. These composites are strong enough to withstand the forces of motors or propulsion systems, but can easily transform, allowing the machines to adapt to their environment.”
The researchers believe, in the future, morphing composites will play an important role in the field of soft robotics and will allow for the creation of multifunctional machines, capable of self-repair after being damaged.
Translated from Robotique molle : Une équipe de l’Université Virginia Tech a créé un robot qui se transforme grâce à un alliage en fusion