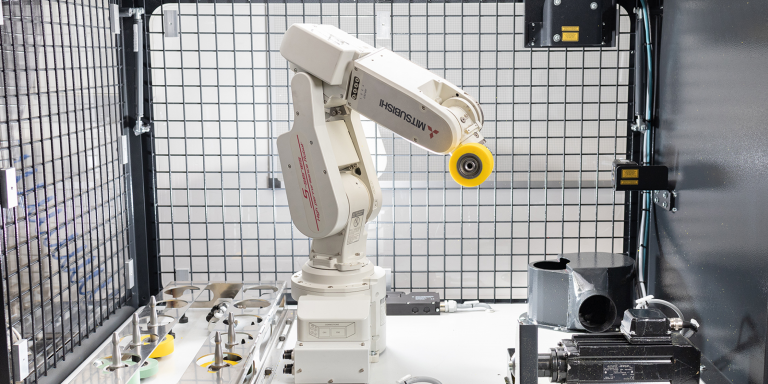
Currently, although entrepreneurs are aware of the potential of artificial intelligence to increase their competitiveness, many are hesitant to take the plunge, doubting the reliability of AI solutions. The Fraunhofer Institute for Mechatronic System Design (IEM) aims to build trust in artificial intelligence systems. Its teams have combined AI and control technology to create a fully reliable system – RoboGrinder, a grinding machine that eliminates up to 40 percent of grinding processes.
The Fraunhofer-Gesellschaft, founded in Munich on March 26, 1949, by representatives of industry and academia, the Bavarian government, and the Federal Republic of Germany, has 76 institutes and universities in Germany focusing on various fields of applied research in which it has become a leader and about 30,000 employees, mostly engineers and scientists. It is a pioneer in innovative products and holds numerous patents. 70% of its revenues come from contracts with industry or specific contracts with the government.
The Fraunhofer Institute for Mechatronic Systems Design
Mechatronics is the synergistic and systemic combination of mechanics, electronics, automation and real-time computing. It is used in all major industrial sectors: transportation, consumer goods, capital goods… Robots, autonomous vehicles, ABS, hard drives, intelligent washing machines… are examples of mechatronic systems.
Researchers at Fraunhofer IEM have set themselves the goal of countering skepticism and increasing confidence in artificial intelligence, in particular by means of a technology for monitoring these systems.
Steven Koppert, head of the Trusted Machine Intelligence group at Fraunhofer IEM, explains:
“We are combining proven control technology with new artificial intelligence. While much of the control technology is based on physical and mathematical models that can be analyzed and trusted, artificial intelligence – which in itself is not particularly trustworthy to begin with – is usually based exclusively on data and also solves creative tasks.”
RoboGrinder: the intelligent grinding machine designed by the Fraunhofer Institute IEM
RoboGrinder is a concrete example of the reliability of an automated system incorporating AI. The institute designed it for Düspohl, a mechanical engineering company.
Until now, the very complex shaped profile packaging rolls that need to be ground frequently were ground manually there, because automation using only control technology is not easily feasible for the rubbery material. Indeed, the material of the roller is so elastic that it bounces back after grinding, this behavior is very difficult to model and integrate into a control technology approach. While one would think that by multiplying the grinding processes, it would be easier, the process, on the contrary becomes inefficient. In addition, the surface quality of the rollers may deteriorate with the number of grinding processes. The use of AI solves these problems.
Steven Koppert explains:
“We document all grinding errors that occur during each grinding process and use it to train an artificial intelligence model – so the AI takes over the correction, especially during fine adjustments. Comparatively, you could say that the control technology serves as a guardrail, while the artificial intelligence ensures that the curve in the road is negotiated in the best possible way.”
Thus, the process can be reliably automated, which is a first. Profile coating companies in the building components and furniture industry, will be able to reproduce spare parts themselves in their factories, with the prototype measuring only one by two meters, within minutes.
Uwe Wagner, managing director of Düspohl, states:
“With the help of our machines, our customers in the building components and furniture industry produce a wide range of different models and components. At the same time, they must be able to react quickly and easily to the circumstances of new orders. The intelligent grinding system would therefore be a major component of the automation.”
Reduction of grinding processes by up to 40 percent
The Fraunhofer IEM researchers began by digitally mapping the grinding process. According to the researchers, ” RoboGrinder can eliminate 15 percent of the grinding operations when resharpening from the approximate size to the specified size. The benefit becomes even more apparent when resharpening used rolls, where the grinding process takes place directly on the sensitive area – meaning that resharpening must be done with extreme care so as not to remove too much material.”
Steven Koppert states:
“With the digital twin, we were able to show that we could eliminate up to 40 percent of the grinding process.”
Thanks to RoboGrinder: the specified size is adhered to, the shape of the workpiece is detected independently by a laser scanner, and another advantage is the very fast automated machining process
Researchers are currently conducting parametric studies and working on construction-related issues, among others. The first RoboGrinder prototypes will be presented at the Hanover Fair at the end of May.
Translated from Les chercheurs de l’Institut Fraunhofer IEM présentent RoboGrinder, première rectifieuse intelligente